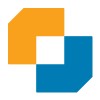
Matchtech
Quality Engineer (Remote)
Quality Engineer | Matchtech | UK
Looking to join an Innovative company? The company not only produceproducts which are used in some of the most challenging environments in theworld but have a number of awards under their belt!
Overview
Important: All applicants must be able to obtain Security Clearance*minimum 5 years UK residency*
Working: Possible Flexible and some remote working potentials.
...Quality Engineer | Matchtech | UK
Looking to join an Innovative company? The company not only produce products which are used in some of the most challenging environments in the world but have a number of awards under their belt!
Overview
Important: All applicants must be able to obtain Security Clearance *minimum 5 years UK residency*
Working: Possible Flexible and some remote working potentials.
❓ Want to join a successful business who are passionate about solve their customers’ problems, providing engineering solutions to safety and mission critical challenges in the air and on the ground?
❗ A trusted business, who’s solutions can be found in the latest military aircraft and vehicles, in civil aircraft, and in unmanned vehicles.
🏆 The company have a number of awards, most recently been named as an Award winner (Gold Award) in MoD Defence Employer Recognition Scheme!
The Quality Engineering function is responsible for ensuring the effectiveness and fulfilment of the quality policy, which is to comply fully in the conduct of the Company’s business with all applicable regulatory and customer required specifications, and to maintain an effective Quality Management System.
Working in partnership with the Operations and Engineering teams to ensure that products and processes conform to applicable standards and specifications, and the incidence and costs of quality non-conformances are constantly monitored and improved, while maintaining the highest practicable standards of manufacturing productivity and efficiency.
Responsibilities:
Plan and carry out a schedule of audits and assessments with completion of associated documentation and activities in accordance with the QMS
Support of any investigations arising from Quality issues through to their documented conclusion, with supporting root cause analysis and solutions to prevent re-occurrence
Manage completion and effectiveness of Corrective and Preventative measures
Ensuring Quality measures with associated targets are maintained for QA Compliance
Support of external Quality audits, assessments and visits by customers and authorities
Ensuring that regular shop floor checks are performed, reported and any associated issues are effectively resolved
Support in the coordination and facilitation of timely responses and resolution of quality issues identified
Assist with the generation of Quality Plans and proposals
Support in the generation of First Article Reports internally as well as any associated customer facing activities for product verification.
Support customer or supplier Source Inspection or Delegate Product Review Verification activities
Facilitation of concession applications and engineering change requests
Participate in Engineering Design Project reviews and auditing these projects to ensure compliance to internal QMS requirements
Participate in Contract Reviews and New Business Proposal launches
Support Operators Approval Processes, including issuing of Stamps and Scopes of Approval
Ensure the departmental objectives are achieved in line with the job holders individual objectives
Perform duties in accordance with company policies, procedures and processes
Develop and support of a business improvement culture and associated activities e.g. process mapping, lean, continuous improvements etc.
Assist with the maintenance of company approvals e.g. EASA/CAA, FAR, ISO, AS etc. to maintain airworthiness
There may be additional activities to perform from time to time in order to maximise the contribution to goals and objectives.Experience needed:
Has a proven range of Quality/Business Improvement experience
Proven experience working within a quality management system
Experience with auditing, both internal and supporting external audits
Knowledge of manufacturing environment and working with a supply chain
Experience of liaising with internal and external customers
Good communication skills demonstrated both verbally and in writing in the form of presentations and recommendations for improvement
Works effectively with others
Demonstrated experience in building good working relationships and gaining trust and respect with internal and external customers
Plans work and delivers on time
Demonstrates a “Can do” positive attitude
Use own initiative within the scope of the role
Makes timely decisions within the scope of the role
Proactively able to manage own work to in order to achieve objectives
Good application of Microsoft packages and relevant software for the role (Microsoft Outlook, Excel, Word and PowerPoint) Desirable:
Has worked in an Aerospace Organisation, Experience in:
Aerospace quality standards (e.g. AS9100, EASA Part 21, Part 145 etc)
Other aerospace topics e.g. FOD, counterfeit avoidance etc.
First Article / Parts Approval reporting methods (E.g. AS9102, PPAP etc.)
Process Measurement techniques (e.g. SPC, KPIs, etc .)
Quality Management System and Process Mapping Software
Certified Quality Auditor training
Education linked to Engineering Qualifications
Educated to at least A level at grade C or above (or equivalent), ideally educated to degree levelFor full information, please get in touch.
Related Jobs
See more All Other Remote Jobs-
NewSave
-
NewSave
-
NewSave
-
NewSave
-
NewSave
-
NewSave
-
NewSave
-
NewSave
-
NewSave